Forja a cielo abierto
En la forja a troquel abierto, un martillo golpea y deforma la pieza de trabajo, que se coloca en un yunque estacionario. La forja a troquel abierto recibe su nombre del hecho de que las matrices (las superficies que están en contacto con la pieza de trabajo) no encierran la pieza de trabajo, lo que permite que fluya, excepto cuando las matrices entran en contacto con ellas. Por lo tanto, el operador necesita orientar y posicionar la pieza de trabajo para obtener la forma deseada. Las matrices suelen ser de forma plana, pero algunas tienen una superficie especialmente diseñada para operaciones especializadas. Por ejemplo, una matriz puede tener una superficie redonda, cóncava o convexa o ser una herramienta para formar orificios o ser una herramienta de corte. Las piezas forjadas a troquel abierto se pueden transformar en formas que incluyen discos, cubos, bloques, ejes (incluidos ejes de paso o con bridas), mangas, cilindros, planos, hexes, rondas, placas y algunas formas personalizadas. La forja a troquel abierto se presta para tiradas cortas y es apropiada para trabajos de arte y trabajos personalizados. En algunos casos, la forja a troquel abierto puede emplearse en lingotes de formas rugosas para prepararlos para operaciones posteriores. La forja de matriz abierta también puede orientar el grano para aumentar la resistencia en la dirección requerida.
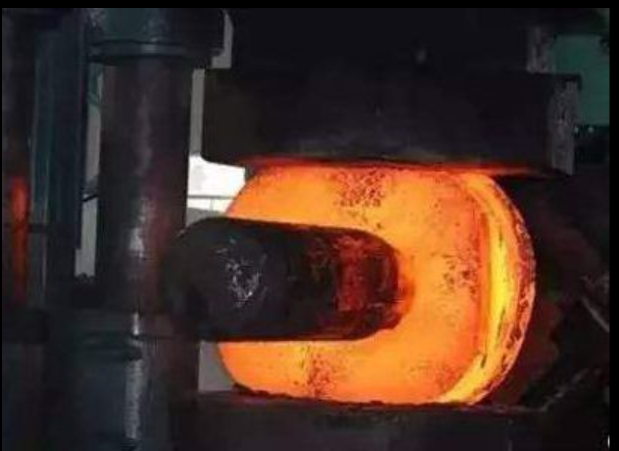
Forja estampada
En la forja de estampación, el metal se coloca en una matriz que se asemeja a un molde, que está unido a un yunque. Por lo general, la matriz de martillo también tiene forma. Luego, el martillo cae sobre la pieza de trabajo, lo que hace que el metal fluya y llene las cavidades del troquel. El martillo está generalmente en contacto con la pieza de trabajo en la escala de milisegundos. Dependiendo del tamaño y la complejidad de la pieza, el martillo se puede soltar varias veces en rápida sucesión. El exceso de metal se exprime hacia afuera de las cavidades del molde, formando lo que se conoce como "destello". El flash se enfría más rápidamente que el resto del material; Este metal frío es más fuerte que el metal en la matriz, por lo que ayuda a evitar que se forme más flash. Esto también obliga al metal a llenar completamente la cavidad del troquel. Después de forjar, se retira el flash.
Forja molesta
La forja molesta aumenta el diámetro de la pieza comprimiendo su longitud. Basado en el número de piezas producidas, este es el proceso de forja más utilizado. Algunos ejemplos de piezas comunes que se producen con el proceso de forjado en mal estado son válvulas de motor, acoplamientos, pernos, tornillos y otros sujetadores.